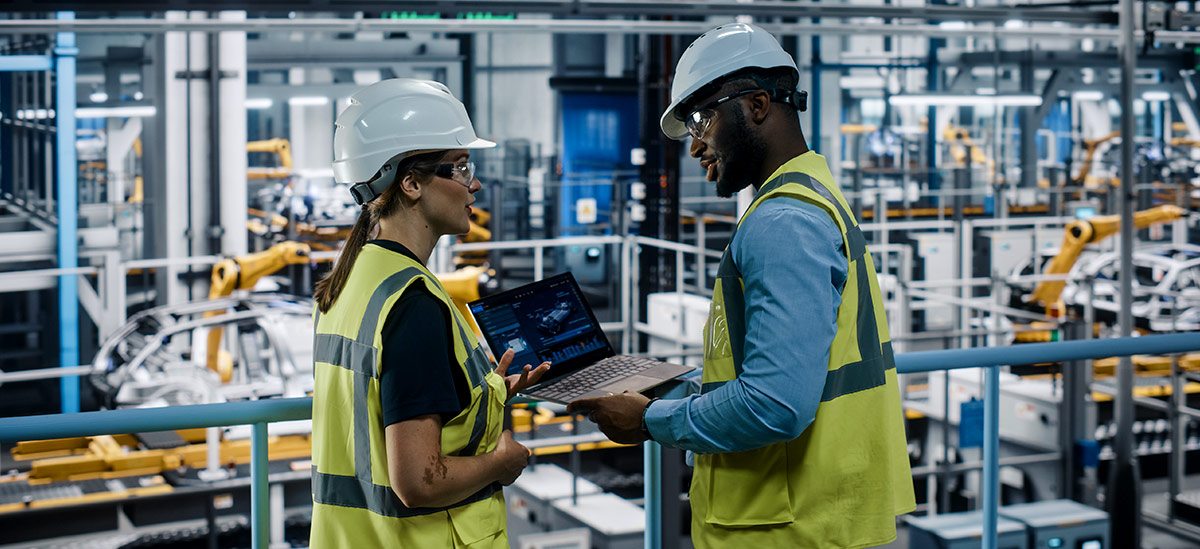
Years into the Fourth Industrial Revolution — Industry 4.0 — manufacturers feel squeezed by growing customer and employee expectations. Consumers increasingly flock to brands that can offer a tailored, "always-on" customer experience. But amid the Great Resignation, the talent needed to deliver this type of experience has become harder to come by — and workers are looking for employers who value work-life balance and put their staff 's wellbeing first.
As a result, manufacturers must look to innovative solutions to help close this "expectations gap," and their automation can help. Automation offers a dual benefit for employers: it can help create the seamless customer experience that customers crave and allows employees to focus on the most meaningful work.
Here, we will discuss how automation is elevating the customer experience and enhancing productivity in manufacturing — and how companies can set themselves up to succeed with automation in the future.
Using automation to enhance the customer experience
Manufacturers looking to stay ahead of the customer expectations curve need to embrace digital transformation — and automation can help companies create an outstanding customer experience. Automation can allow customers to send digital payments, making payments quicker and more convenient and allowing customers to manage their accounts anytime, anywhere.
An automated customer service platform can also leverage chatbots to answer customers' questions and resolve lower-level concerns, identify cases to elevate to a customer services representative, and track the left cycle of each ticket so agents can get up to speed and help customers resolve their issues quickly.
Improving efficiencies via automation
Working in Industry 4.0 calls for leveraging automation to streamline work flows — offloading tasks that can be automated to machines so that the team can pursue the most meaningful work.
Sensors can play a pivotal role in helping facilities function properly: they can monitor performance and detect failure patterns so that staff can implement maintenance schedules based on the equipment's condition rather than at fixed intervals. Innovations in 3-D printing allow manufacturers to build products, components or prototypes quickly, efficiently and with minimal waste. And robots can be used to perform increasingly-precise tasks, allowing workers to focus on tasks that require a human touch.
Reshaping strategies with data-driven decisions
Automation paired with machine learning and artificial intelligence can prove valuable for manufacturers. Deep learning algorithms can sift through mountains of data to find patterns, helping companies set data-driven benchmarks and goals against which to measure their success.
Machine learning can also help manufacturers create forecasting models, allowing companies to predict how challenges like supply chain disruptions or inflation may impact their business. Finally, machine learning can help companies scenario-plan and model new ways of doing business — for example, identifying ways to work more sustainably — so companies can make data-backed decisions as they look to the future.
Looking to the future: The importance of talent
As automation continues to the manufacturing landscape, manufacturers need to optimize technology and human capital to succeed. Employees can prove invaluable for leveraging automation effectively, offering insight into how best to re-engineer processes to address bottlenecks, work more productively and improve quality.
This means that, as companies embrace automation, they must also focus on finding the right talent. As Deloitte reports, "soft" skills — such as creativity and management skills — will be most in-demand, as workers are called upon to turn automation-backed insights into collaborative action. Tomorrow's workforce will also need a strong digital skillset to make the most of emerging technologies.
In a competitive labor market, this means manufacturers must think ahead and identify the skills they need early. However, those who do it well can assemble the team they need to thrive — now and in the future.